The roofing installation process can be messy, especially when removing old shingles. To prevent plants, siding, gutters, window screens and outside condensing units from being damaged, the crew will cover them with tarps.
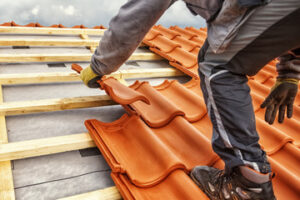
The crew will also lay the ice and water barrier and run underlayment. Then they will shingle your roof, including around chimneys and skylights. For professional help, contact Palm Coast Roofing Companies.
The roof over your head is more than just a protective shelter. It’s a crucial design element that helps boost the aesthetics of your home and enhance its energy efficiency. But with the plethora of roofing materials available, choosing one to suit your needs and budget can be overwhelming. There are several factors that should be taken into account, such as the climate in your region and the durability, cost, maintenance requirements, and energy efficiency of each material.
Asphalt shingles are one of the most common roofing materials in the United States, and they offer a wide range of colors and styles to complement any style. Generally, they last about 20 to 30 years and provide a good balance of durability and affordability. Other popular options include concrete tiles and clay tiles, which are a great choice for hot climates but can become fragile in cold weather conditions.
Slate is another luxurious roofing material that’s often used on historical or rustic homes. This premium option offers a unique aesthetic that can be an attractive accent to any house. It also helps improve a building’s insulation and provides protection against mold, mildew, and fire. However, it’s important to note that slate is a heavy roofing material, and it’s typically installed one piece at a time.
A variety of tools are used in a typical roofing job, including a nail gun for speedy and precise installation, a roofing knife for cutting shingles to size, and a roof ripper for quickly removing existing shingle material. Additionally, it’s crucial to have the right roofing sheathing in place to protect against moisture and prevent leaking.
For flat roofs, special materials are needed to ensure water doesn’t pool on the surface or leak into the building. These materials may include EPDM, a synthetic rubber sheet material or TPO, which is a blend of polymers that’s designed for low-sloped roofing systems. They also may include a built-in drainage system, such as ridge vents and soffit vents, which help direct rainwater away from the roof to avoid structural damage and mold growth.
Preparation
Before the roofing installation begins, your roofer will clear the area of any debris or obstructions. This is crucial to a successful restoration and makes sure the crew can move freely without worrying about hitting anything they shouldn’t. The contractor will also inspect the surface of your roof to make sure it’s free of any rust, dents, or other damages that could interfere with the coating adhesion.
Next, they’ll cover your roof with underlayment. The underlayment will protect the underlying layers of your roof, keeping water from seeping into the interior of your home. It will be nailed down to the decking and shingle layer, with a nail every four to six inches along the edge and closer near the ridge of your roof.
If you have any roof accessories like solar panels, satellite dishes, or skylights, these will need to be removed and reinstalled after your new roof is completed. Your roofer will also waterproof any valleys, which are the corners of your roof where the slopes meet. They’ll use a special material to ensure these areas are well-covered.
Once the underlayment is in place, your roofing contractor will install shingles or metal panels. They’ll start at the top and work their way down, overlapping each row as they go and nailing them in. They’ll also use a special cap nail in the corner of each shingle to keep rainwater from leaking into your home.
At this point, your roofer will also replace any vents that allow air to pass through your roof into your home’s interior. This may include sewer ventilation, curved vents for bathrooms or kitchen ranges, and more. Your contractor will seal these vents with a strong adhesive to make sure no water is able to enter your home from the rooftop.
Now’s a good time to take down any wall-hung decorations and to relocate fragile items to a safer location in your home. The pounding of hammers and impact from the nails will cause vibrations that can damage furniture or other delicate items. Also, consider covering any valuables in your attic with plastic tarps or moving them to a secure spot for the duration of the project.
Installation
The roofing contractor will start by installing a layer of underlayment. This is a water-resistant material that is installed over the roof deck before the shingles are placed on top of it. It will be nailed down to the roof sheathing using cap nails, with close nails along the edge and then spaced out more towards the middle. The roofing contractor will also install drip edge flashing, valley flashing, and ice and water sheathing at this time. Other flashing will be added around chimneys, wood stove pipes, vents, eaves, and hip roof areas. This will prevent water infiltration and damage to the interior of your home. It will also help to improve attic ventilation and energy efficiency. Roofing vents are usually placed in the attic, but curve and ridge vents may be installed for sewer ventilation and kitchen or bathroom exhausting purposes.
Final Inspection
The final inspection is the last step before local building officials sign off on your work and give you the green light to apply for a certificate of occupancy. This is a very important stage, and you’ll want to avoid any surprises.
Having an experienced inspector on your side can make all the difference. They can point out potential issues that you may not have noticed, and help ensure everything is done according to codes and regulations. They’ll also catch any mistakes that could lead to costly repairs down the line.
While the specifics of a final inspection depend on your particular project, there are some general tips that can be used to prepare for any type of inspection. For example, make sure all necessary documents have been submitted and that all contractors are prepared to answer questions from the inspector. It’s also important to schedule the inspection at a time when the construction site is clean and accessible, with no one in the way or working on any other projects.
It’s also recommended to prepare a checklist that can be used during the build to verify that all items are completed and ready for the inspection. Adding photos, comments, and signatures to this checklist makes it easier to keep a record of progress throughout the project. It’s also important to communicate with the inspector ahead of time to understand what they will be looking for during the final inspection and any specific issues that need to be addressed.
Failing a final inspection can cost you money and can potentially delay your project completion, so it’s vital to be as prepared as possible. A professional inspector will be able to identify issues that you might not have noticed, and help you find solutions quickly so you can get back on track.